
Typically, any discussion of actively removing carbon dioxide (CO2) from the earth’s atmosphere to help reduce the greenhouse effect of manmade emissions has so far centered on carbon storage and capture. That usually means removing CO2 from the waste stream at a high-emission generation point (for example, a power plant) and then putting it into long-term storage, such as by pumping it far underground.
The problem with that approach is that it layers costs upon costs, with only very diffuse benefits. That makes it really difficult to get off the ground in any scalable way.
What if instead, our elevated levels of atmospheric CO2 were viewed as a business opportunity? That’s the approach that the folks at AirCapture LLC, based in Berkeley, California, are taking. Their mission is to use their Direct Air Capture (DAC) technology to pull CO2 straight from the atmosphere, anywhere it’s needed for other industrial processes. “We’ve developed technology to separate CO2 from the air, and to do it in a way that gives our customer a more reliable supply, with no trucking of CO2,” said Matt Atwood, AirCapture’s founder and CEO. “The way we do it is by using contactors similar to what’s in the catalytic convertor in your car. The applications can be anything from food and beverage processing to food packaging to synthetic fuels. And we have support from the Department of Energy, the Department of Defense, and European nations. We’re commercializing our process now. We aim to be price-competitive with other CO2 sources.”
An integral part of developing the company’s technology has been 3D printing, or additive manufacturing (AM). “We’ve used it a number of ways,” said Atwood. “We did rapid prototyping of our injection-molded parts, to make sure we like how they work and how they fit. We were able to rapidly iterate our processes to get our CO2 to the market most sustainably and at the lowest cost. And we were able to explore different surfaces and materials for our parts more rapidly. Additive is more complex, but allows us to make more efficient systems in smaller packages. Our business model is for consolidated, hyper-localized systems. The scalability from additive is where 3D Systems comes in.”
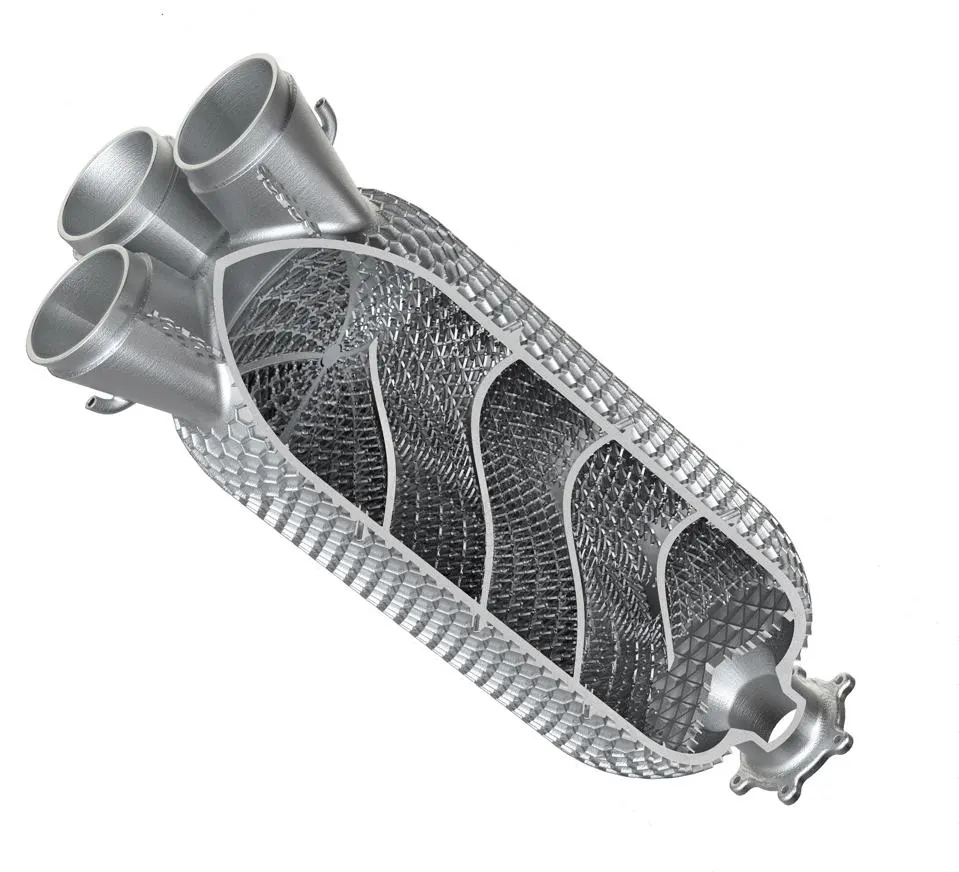
“Think about mechanical filter. They exist today all over the world in many shapes and sizes,” said Scott Green, Principal Solutions Leader at 3D Systems. “Off-the-shelf components are made with mechanical forming. But 3D printing offers a superior way to make them–for example, allowing us to form a more efficient lattice. And not just any lattice, but through computational analysis, and generative design an ideal lattice can be made which presents the least pressure drop and the maximum contact area… this is a key target zone for Direct Air Capture systems. The same goes for heat exchangers, which can be made much more compact but also more efficient, and tailored for a specific problem. The other companies that have been trying to do this are in industries like oil and gas. They’re big companies and they move very slow. And the typical business, and R&D velocity for very large companies can be become an anchor, hindering iteration, failure and learning. One advantage 3D Systems has is that we have the experience across many industrial segments such as aerospace and power generation which allows us to take novel geometry and concepts which work in more developed segments and apply them here in Green tech. Additionally we take great pride in leading the charge in the additive manufacturing industry in taking actionable steps to improve climate. Matt is very agile, doing rapid iterations with rapid failure, then figuring this out. His final design is decentralized and local.”
That leads to a modular product that becomes easily scalable and readily installed by the end user. “Our machine is about the size of a large refrigerator. Our financials are built around proximity to the CO2 user, as well as eliminating the cost and CO2 created in transport with the old model.”
While the immediate business opportunities are the traditional industrial users of CO2, AirCapture sees others on the horizon. “Our opportunities run the gamut from industry to R&D and testing,” Atwood said. Our goal is to scale up our manufacturing as quickly as possible. There’s lots of interest in this technology. These are fantastic things for us to be working on–as the scale goes from hundreds of thousands to millions of units, it will help industry solve problems.”
“In order for us to have a livable planet, the size of the decarbonization industry has to match the energy industry,” added Green. “Also, to solve different problems, different manufacturing solutions are needed. We’ll see massive production from AM. This is the type of accelerator that will make AM super-exciting in the next 10 or 20 years, in both technology and materials.”
For Atwood, it goes back to seeing the business opportunity in helping the environment. “From my perspective, decarbonization will be a rapidly growing market,” he said. “There will be many businesses created that will have good economics, with good job creation, plus decarbonization.”
Comments