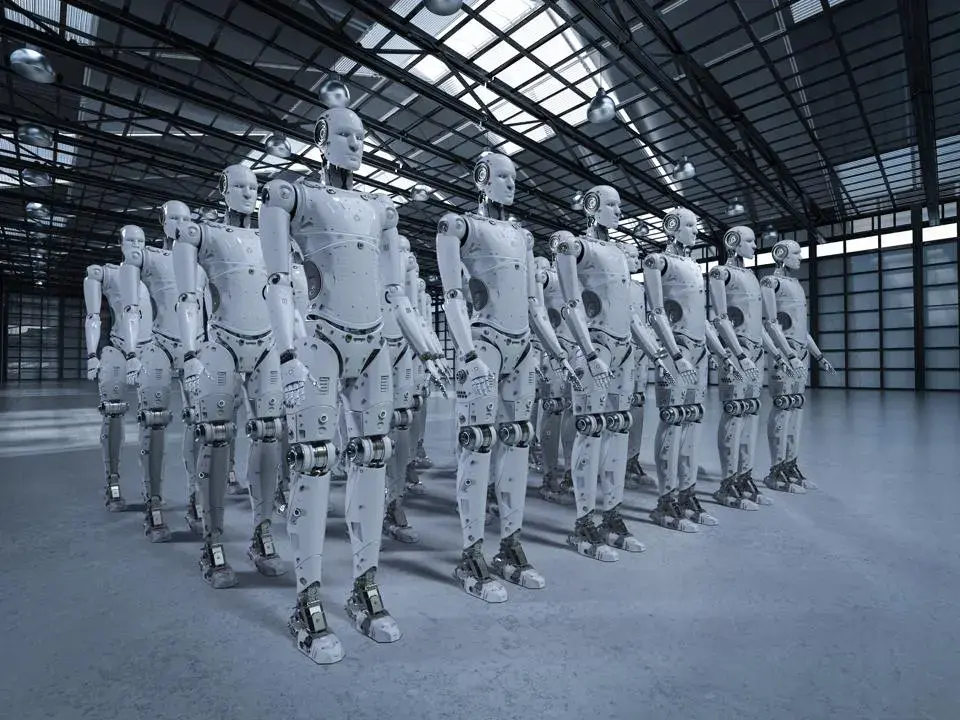
Conventional wisdom has it that a coming onslaught of industrial robots will throw millions of current factory workers out of their jobs. The direst predictions envision whole classes of people permanently locked out of the working world.
As I detailed in one of my earliest articles, robots eliminating manufacturing jobs is nothing new. It’s been going on for decades. But as technological development accelerates and robots become better and cheaper, the risk to current employment is intensified. But that’s not the whole story. Some jobs will be eliminated, certainly – but some will be changed, and new ones will be created.
Nicola O’Byrne, Marketing Manager, Connected Motion and Robotics, at Analog Devices Inc. (ADI), has worked in the industrial automation world for over 20 years. Her current focus is helping companies with insights into how to manage their automation transitions. She thinks that some of the perceived threats are overblown, and that the real risk is in companies and workers failing to understand the challenges of the changes coming, and in the lack of preparation for the future of work. “I think a lot of the media content is dominated by the scare tactics,” she said. “That’s frustrating, and we should be helping counter that. One of the taglines we use is, ‘Making a difference,’ which we see as helping to make employees’ lives better.”
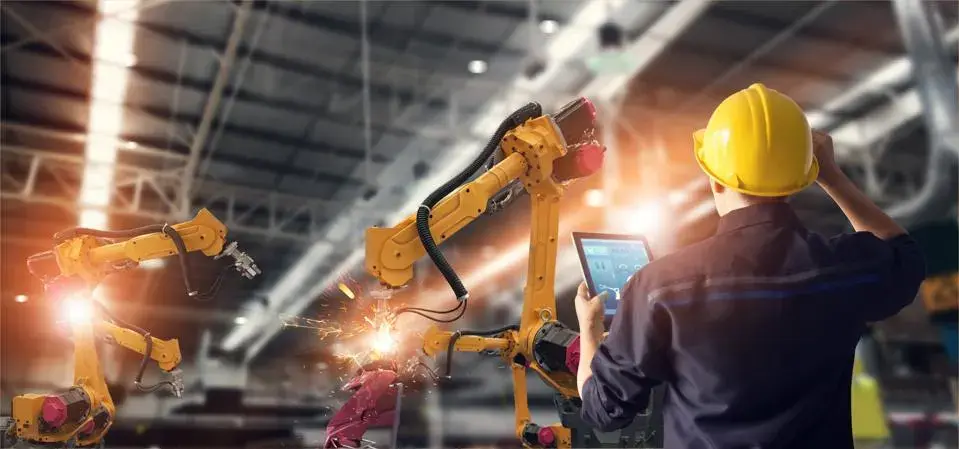
First, O’Byrne feels we should be stressing how newer robotics applications can help create work. Until recently, for example, robots were unwieldy and dangerous, and therefore displaced workers for their own safety. But today’s technology is different. “Unlike legacy robots, where what they did was very exclusionary, new cobot [collaborative robot] technology is designed to work with people,” she said. “That might give new opportunities to lower-skilled workers. Cobot companies are making a real effort to design a more inclusive working environment.”
Like industrial robots, artificial intelligence (AI) is also criticized as a job stealer, but it’s fundamental to those job-creating and job-enhancing opportunities. “AI inspires a lot of fear,” O’Byrne pointed out. “But it can help us emulate sensory motor skills. That will be critical as cobots work alongside humans. It will help with power and force limitations, and sensors for touch and proximity.”
O’Byrne believes cobots offer an additional job creation opportunity that’s rarely mentioned. “Cobots can also potentially open up industrial jobs to people who can’t currently do them – the less-abled, older workers, and so on,” she said.

To be ready for the transformation of manufacturing work will take a different mindset, however. A central element that O’Byrne sees is in retraining and upskilling our existing workforce, while preparing our future workers for higher-level and different work. “The pace of retraining and upskilling needs to quicken,” she said. “It could call for public-private partnerships.” More fundamentally, she believes we need a better understanding of what jobs are at risk. “Tech won’t replace crafts,” she said. “Other jobs will be reshaped or newly created. Robotic programming is a good example – it used to require highly specialized, high-level skills. Today’s technology has made it much more accessible. This could be a real opportunity for displaced floor workers, who have a great understanding of line operations.”
She feels there’s a gross misunderstanding of other elements of what’s coming with industrial automation. “We need to focus on the human skills that can’t be mimicked – empathy and creative thinking, for example.” This is another area where she touts training our current workers for the jobs of the future. “I think when people think of upskilling, they picture getting rid of the old, and bringing in the new. But an operator on the line has process knowledge that can’t be replaced. They’re easier to train than ever for higher-level work.”
Because the brute force or rote work jobs are the ones most likely to be taken over by automation, O’Byrne sees another potential benefit. “This can really help with our shortage of manufacturing labor,” she explained. “Technology can make industrial jobs safer and more pleasant. That will make recruitment and hiring that much easier.”
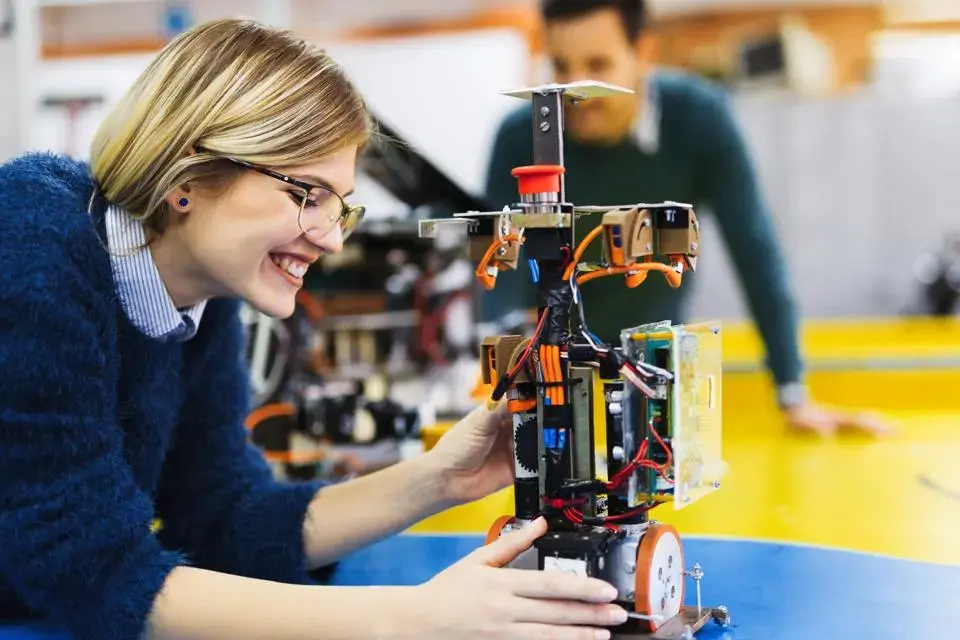
Technology can even help with getting where we need to go when it comes to retraining and upskilling. “AI and augmented reality will offer great new tools to help train people,” said O’Byrne. “They can provide new tools to help guide a person through hands-on learning. At the same time, they can gather data on how well they’re progressing.”
She sees a final opportunity in those places that have seen manufacturing offshored to lower-cost countries. “Technology offers real benefits when it comes to onshoring or reshoring manufacturing work,” she said. “It increases the flexibility of our manufacturing systems to do different things, and the upskilling of the workers makes domestic labor costs much more competitive.”
The new world of industrial automation will reshape manufacturing in other ways. “There’s a huge amount of investment in machine health and reliability,” said O’Byrne. “Quality will be improved as well, as we make advances in precision, speed and motion control. And we have one person at ADI focused entirely on functional safety, helping develop new safety standards for robots.”
In the end, it’s really the same old story. Change is threatening and frightening, so the doom-and-gloom prognosticators are having their day. And rapid change is certainly on the way in the manufacturing technology world. But the reality isn’t likely to be anywhere near as bad as the juicy headlines predict – and in many ways the future is rather bright.
Comments